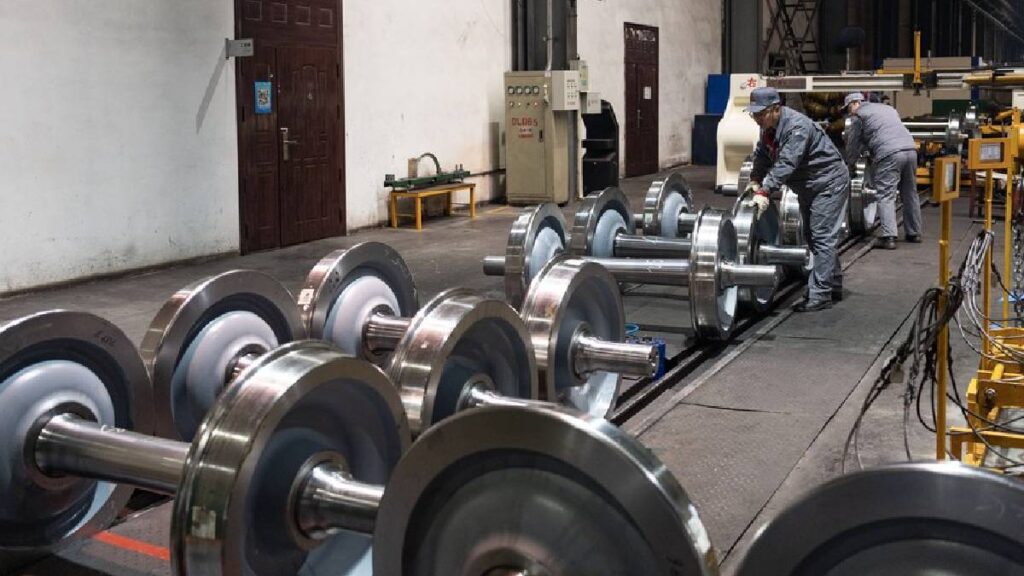
Un equipo de científicos internacionales rompió el cuello de botella tecnológico causado por las propiedades de mala resistencia a la fatiga de los materiales impresos en tres dimensiones (3D). Así que propuso una estrategia innovadora para fabricar una aleación de titanio antifatiga a través de la impresión 3D sin vacíos.
De acuerdo con un estudio publicado en la última edición de la revista académica Nature, la ventaja de la impresión 3D, o la tecnología de fabricación aditiva (AM, siglas en inglés), había sido gravemente comprometida por el pobre desempeño de fatiga de los materiales impresos en 3D bajo cargas cíclicas. Lo que resultó de la presencia de los microvacíos inducidos por el proceso de impresión predominante.
[TE INTERESA: Para evitar incendios: China pedirá estacionar bicicletas eléctricas al aire libre]
¿Cómo se produjo el titanio antifatiga?
Para resolver el problema, el equipo de investigación dirigido por los profesores Zhang Zhefeng y Zhang Zhenjun del Instituto de Investigación de Metales de la Academia de Ciencias de China, trató de producir con éxito una aleación de titanio aproximadamente libre de vacíos Ti-6Al-4V. Mediante el desarrollo de una nueva técnica de procesamiento de impresión 3D para regular por separado la microestructura y los defectos.
La nueva técnica, conocida como el Proceso de Fabricación Aditiva en Red, incluye la presión isostática en caliente para eliminar los microvacíos y el tratamiento térmico posterior de alta temperatura y en tiempo corto para restaurar la microestructura de AM con un listón de martensita fina. Para que puede restablecer con éxito una microestructura de AM en red casi sin vacíos a la aleación de titanio.
El grupo confirmó la resistencia a la fatiga de tal aleación de titanio de impresión 3D sin vacíos. Descubrió que sobrepasó el nivel de resistencia de todas otras aleaciones de titanio de impresión 3D y forjadas, así como la de otros materiales metálicos. “Esta investigación ha revisado el entendimiento previo de la comunidad sobre el mal desempeño de fatiga de los materiales impresos en 3D y se espera que avance la aplicación de tales materiales en el campo aeroespacial y otros sectores”, manifestó Zhang Zhefeng.